First, what is an LNG jetty?
An LNG jetty is a construction projecting pipelines from an onshore terminal out over water. It often consists of piles, a trestle, pipelines, access road, loading arms, and breasting and mooring dolphins. The process of designing and constructing a jetty can be time consuming, costly, and requires intervention in both onshore and marine environments. A jetty serves as a connection that enables transfer of LNG between a berthed ship and the onshore terminal. Depending on local conditions, the length of the jetty may vary from just tens of meters to several kilometers. A jetty can be combined with different terminal configurations, such as floating storage regasificationunits (FSRU), floating storage units (FSU), floating regasification units (FRU) and onshore terminals, which all commonly utilize a jetty to transfer LNG or gas to shore.
Numerous components and aspects of an LNG jetty
Jetty piling
Piling is the process of setting deep foundations into the seabed. These deep foundations support the jetty topside. An LNG jetty needs to withstand rough conditions, which is why the piles needs to be driven through sand and sediments, deep into the seabed.
Jetty topside
The topside of a jetty is the part of the structure which lies above water that is supported by the piles. The topside typically consists of a trestle with gas pipelines, serving as the connection between the onshore facilities and the jetty head. The jetty head holds the loading arms forloading or discharging LNG to and from the LNG carrier. It also comprises berthing and mooring dolphins used to moor the LNG carrier.
Breasting and mooring dolphins
Dolphins are marine constructions that extends above water level. They are used to extend the berth of the ship by providing extra mooring points. Together with the jetty trestle and the jetty head, the dolphins typically make a T-shape. Breasting dolphins serve to take up some of the berthing loads and as mooring points to restrict motion in the longitudinal direction of the vessel. Mooring dolphins are used for mooring lines only, often to restrict the transverse movement of the berthing vessel. These dolphins are usually connected by walkways for easier mooring line handling.
Transfer line
Pipelines for transferring LNG are placed on the jetty with associated valves, loading arms and safety systems. Loading arms works as the interface between the pipelines and the LNG carrier, and connects to the carrier manifold with the pipelines to shore. Emergency release couplings (ERC) are fitted at the end of the arm towards the vessel manifold and serves to separate the jetty pipelines safely from the vessel in case of an emergency.
Dredging
Dredging is a process utilized in shallow waters to improve accessibility for ships. To avoid running aground, ships require a certain water depth depending on the draught of the ship and the loading condition. LNG carriers typically have a draught of 10 to 15 meters, which sets the standard for the depth of LNG jetties. Tides and waves must also be considered, and a safety margin is always added. If the waters outside the LNG terminal are too shallow, dredging is done to excavate materials from the sea floor beneath the ship berth and in the approach area. A dredger is a floating plant that picks up the sediments and debris from the bottom and removes it mechanically or bysuction.
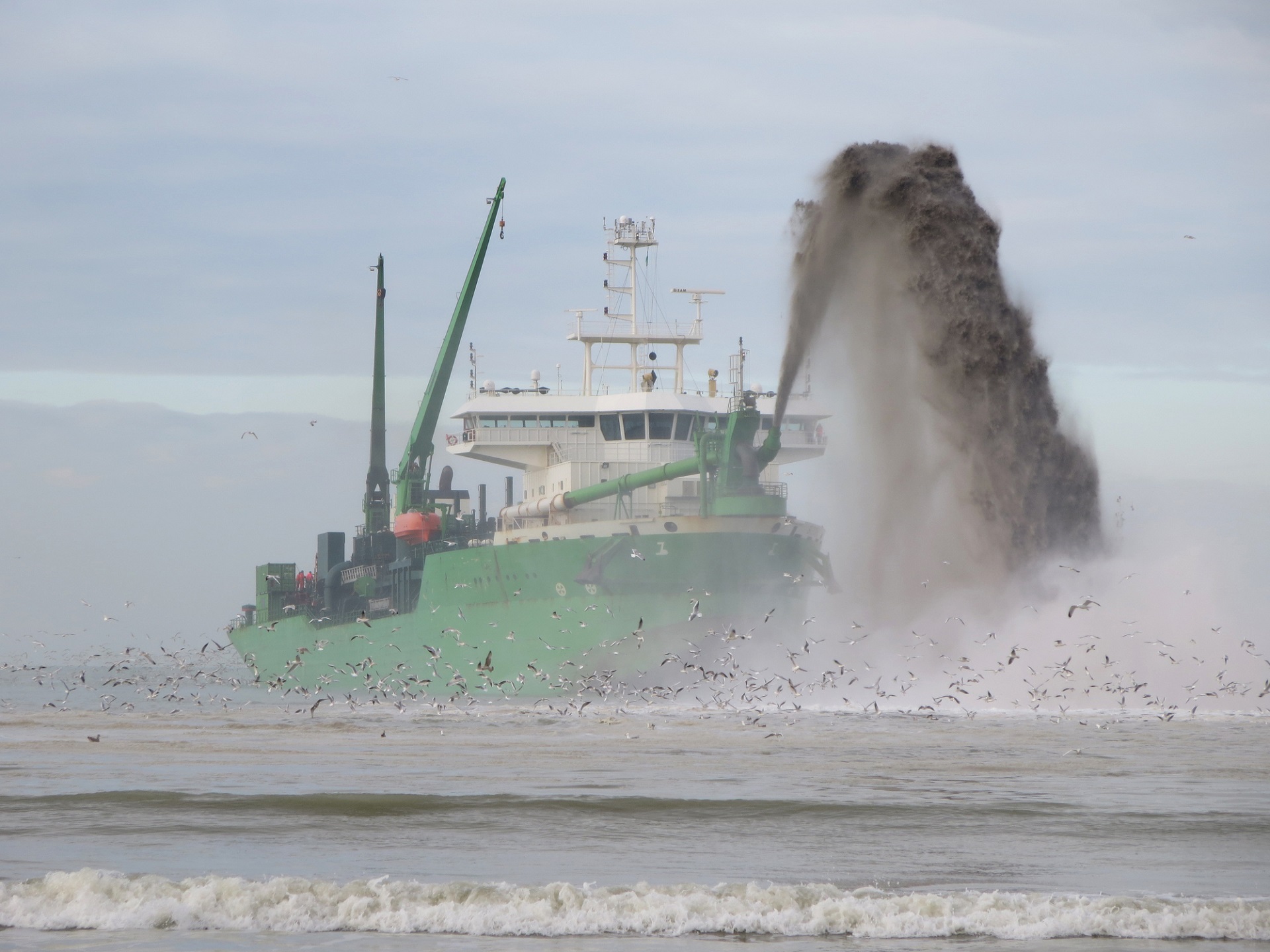
Implications of building a jetty
Not only can LNG plants- and regasification facilities be costly, but a jetty alone will require a substantial initial capital expenditure (CAPEX). Operating costs (OPEX) include work hours spent on personnel operating the jetty during LNG transfer, and numerous tugboats needed to position the LNG carrier correctly and securely.
Carrying out a jetty project is time consuming, potentially ranging from 2 to 5 years in duration. Preliminary work related to the project include activities such as feasibility studies, environmental impact assessment, getting governmental approval, and reaching investment decisions. Once this is in place, the actual construction work on the jetty can start, including necessary dredging and LNG pipeline and equipment production, in addition to any necessary ship fixing or FSRU conversion.
In most cases, dredging is a necessity for the feasibility of LNG transfer from ship to shore. However, due to concern for local wildlife and ecosystems, it is preferable that both dredging and environmental intervention in general is limited to a minimum. A jetty could potentially be of massive dimensions, which again will require vast interventions in both on- and offshore environments. Several jetty projects have proven themselves to be damaging to local environments, as seen in e.g. the Gorgon gas project in Australia.
A jettyless transfer system serves as an innovative solution to the above mentioned implications of a jetty. Read more about jettyless LNG compared to traditional LNG jetty here.